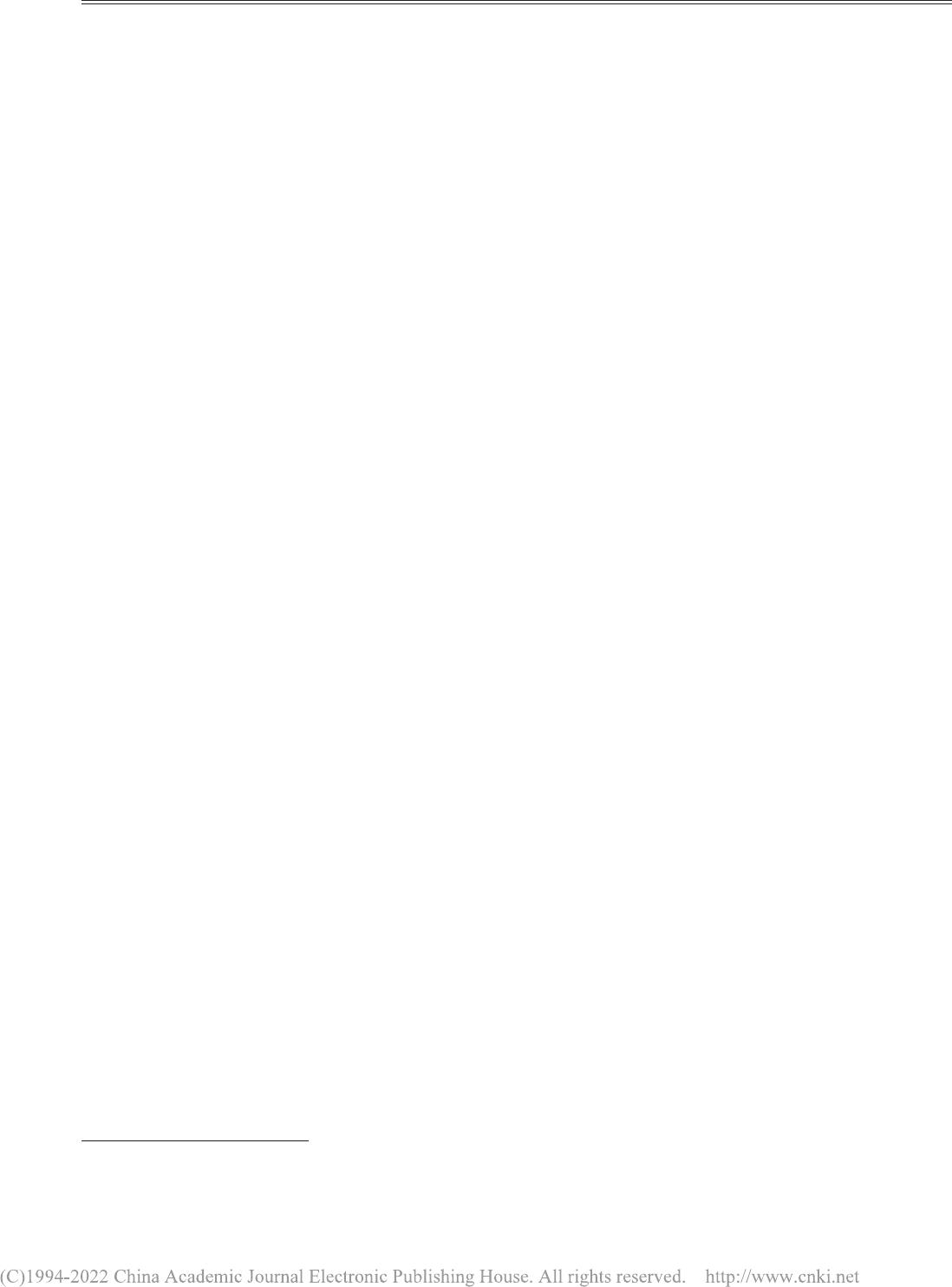
第39卷 第 2期
2018年2月
太阳能学报
ACTA ENERGIAE SOLARIS SINICA
Vol. 39, No. 2
Feb., 2018
收稿日期:2015-12-29
基金项目:国家自然科学基金重点项目(U1137601)
通信作者:马文会(1973—),男,博士、教授,主要从事硅冶金与硅材料方面的研究。mwhsilicon@126.com
文章编号:0254-0096(2018)02-0520-09
冶金法多晶硅光伏系统能量回收期与碳足迹分析
于志强1~3,马文会 1~3,魏奎先 1~3,吕国强 1~3,陈正杰 1~3
(1. 昆明理工大学复杂有色金属资源清洁利用国家重点实验室/真空冶金国家工程实验室,昆明 650093;
2. 昆明理工大学冶金与能源工程学院,昆明 650093;
3. 昆明理工大学云南省有色金属真空冶金重点实验室/云南省高校硅冶金与硅材料工程研究中心,昆明 650093)
摘 要:运用生命周期评价(LCA)方法对我国 1 MWP冶金法多晶硅光伏系统全生命周期的总能量需求、能量回收
期和碳足迹进行计算分析。结果表明:1 MWP冶金法多晶硅光伏系统发电的总能量需求为 1.84×107MJ、碳足迹
1.43×106kg、能量回收期为 3.98 a;总能量需求和碳足迹主要来源于生产阶段,拆解回收处置阶段影响巨大;生产阶
段中,平衡系统及辅件生产影响最大,太阳能级多晶硅生产其次;铝材、电力、工业硅的用量和硅片回收率是影响总
能量需求和碳足迹的关键性因素。
关键词:冶金法多晶硅;光伏系统;生命周期评价;能量回收期;碳足迹
中图分类号:X828 文献标识码:A
0引 言
近 年 来 ,随 着 人 口 增 长 和 经 济 发 展 ,能 源 安
全和气候变化等问题日益严重。当今,世界范围
内应用的 68%的能源都来自于化石燃料,发电是
全球温室气体排放的主要原因,其产生的温室气
体排放约占全球排放量的 40%[1]
。燃烧传统的化
石燃料会带来气候变化、全球变暖、大气污染、酸
雨等一系列的环境问题。为了应对能源短缺和
环境污染的挑战,减缓气候变化,迫切需要发展
可再生能源技术,特别是光伏技术[2,3]。 随 着 技
术发展和生产成本降低,太阳能发电已成为一种
可大规模发展和应用的可再生能源技术,受到了
全世界的广泛关注[4,5]
。
光伏技术直接用太阳能发电似乎非常清洁也
没有环境影响,但从整个生命周期来看,其生产、运
输、运行及拆解回收处置等阶段实际上都消耗了大
量的能源并排放了温室气体
[6]
,“绿色太阳能”背后
的环境问题备受关注。国内外学者对多晶硅光伏
系统进行了生命周期评价或碳足迹分析[7~15]
,但研
究对象多为改良西门子法或硅烷法多晶硅光伏系
统,且未完全涵盖全生命周期所有阶段。本文用我
国生命周期背景数据,计算冶金法多晶硅光伏系统
的能量回收期、全生命周期总能量需求和碳足迹,
以准确辨识各生命周期阶段的环境影响,为我国光
伏发电产业提供决策支持,并完善生命周期评价
(life cycle assessment,LCA)基础数据库。
1研究方法和数据获取
生命周期评价(LCA)作为一种重要的环境管理
工具,用于评估产品或服务生命周期全过程中相关
环境因素及其潜在影响。能量回收期和碳足迹是
两个应用最广泛的环境指标,可用于评估光伏系统
的可持续性和环保性能
[6]
。
能量回收期指一个光伏发电系统全生命周期
内所消耗的能量除以该系统的年平均能量输出,单
位为年。本文总能量需求的评估采用 TKE
eBalance 软件中的一次能源消耗(PED)评价指标。
碳足迹是产品系统整个生命周期产生的直接
和间接的温室气体排放之和,主要以 CO2-eq 为单
位。本文碳足迹的评估采用 IPCC 2007 评估方法中
的GWP 评价指标。
本文数据主要来源于云南、宁夏和江苏相关企
业调研数据及参考文献。
DOI:10.19912/j.0254-0096.2018.02.033